Hall Thruster Erosion Measurement
The Problem:
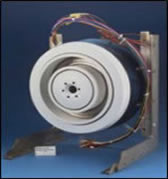
Crack detection in aircraft engine and other high-energy rotating parts is extremely important, because uncontained failures
can result in serious damage to equipment and loss of life. (For an example, see NTSB report NTSB/AAR-98/01). High length-to-diameter
(L/D) bores, like tie-rod holes found in aircraft engine fan hubs, present a particularly difficult challenge for airline NDT
staff. Visual inspection of these small diameter and deep holes can be compromised by poor access, operator subjectivity and fatigue.
- Crack Detection in Aircraft Components
- Mapping Chips in Thrusters
- Micro-Sensor for NASA
The Solution:
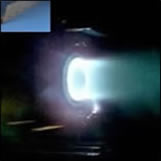
LTC's laser profiling sensors are ideal for applications where precise measurements must be made in a confined space. Unlike typical laser-based surface mapping systems that project a line or spot from a large external source, LTC's LP sensors use laser diodes and miniature optics, making them small enough to reach inside the annular cavity. In addition, the LaserVideo™ image dataset from the laser sensor provides valuable qualitative information about the surface condition.
The Details:
The US Air Force contracted with LTC to adapt the Laser MicroMap™ system to provide three-dimensional maps of both the conical "inner guard ring" and the cylindrical "outer guard ring" of a developmental Hall thruster. LTC provided a system with a custom laser profiling sensor and a three-asix stage-based delivery mechanism, combined with our standard LP-2000™ Control Unit and LaserViewer™ software. This system was able to map virtually 100% of the anode surface, with a spatial of 0.001 inch (0.025 mm) and a depth resolution of 0.0002 inch (0.005 mm).
The images below shows scan data that has been imported into MATLAB™.
Inner Guard Ring
Full 360° Scan of Surface
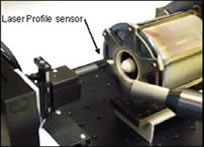
Outer Guard Ring
Section View of Surface
More information regarding Hall Thruster Erosion Measurement.